Rowan Lamont went looking for the bike lifeblood in a petrol-flooded city.
New York City for the first time visitor is an immersion into the land of the motor vehicle. Concrete canyons are riddled with rivers of yellow taxi cabs and frantic delivery vans; the cycle messengers seemingly use a sixth sense to navigate through the noisy flow.
In amongst the hustle of one of the world’s busiest cities are a group of frame builders who passionately ply their trade in the petrol mania. I was more than a little curious to find out what it was that drove them against the tide of engine culture. I was naive to the surprises I was about to unearth as I tripped my way through the Big Apple.

Nestled in a dead end street deep in Brooklyn I met Johnny Coast, and with his dreadlocks dangling we walked to a nearby coffee shop. He has rented a small garage space for his workshop out of the way from everywhere and everyone for the past seven years. Much to his chagrin, developers are moving into the vacant lot next door. “Yeah it kinda sucks because I’m going to start getting passing trade interrupting my work.” Johnny is passionately focussed on hand-building custom Randonneur bicycle frames taking influence from classic “constructeur” builders such as Rene Herse, so he passes potential clients onto other builders if they are asking for anything that deviates from this passion. We sit down with our coffees back in his garage and I begin to understand why. His frames are exquisitely detailed, working purely in steel silver soldering lugs or fillet brazing joins with utter consideration and no unnecessary flamboyance. “I build with the philosophy of the whole bike being one entity, for example, this front rack is made specifically to integrate with the fork and the bike is built to ride beautifully when it is loaded for a ride – it is the complete picture.”
Johnny grew up in an environment that would nurture his desire to design and build, his father made hot-rod motor cars and he could weld by the time he was twelve. He loves solving problems relating to the body, the rider’s needs, and the possibilities open to him using his craft. Building a couple of frames a month, Johnny has a modest waiting list so that he can carefully consider the design and build on a one by one basis. You very quickly ascertain Johnny is comfortable with where he is at, doing what he loves, in a precise and planned manner un-flustered by any hubbub fads and trends. He simply prescribes beautiful bicycles for a niche market of people who love long rides and will celebrate a bicycle made specifically for them. Johnny should be wearing a saffron robe, but jeans and T-shirt are less flamboyant and far more practical.
As is the way in New York everyone knows everyone else, so Johnny rings Seth Rosko, a frame builder who used to share his space. When I arrive the roller door was half open and ducking under I stuck my head into a tiny garage packed to the rafters with tube-sets, jigs, machining equipment and of course bicycle frames. Seth was in the process of welding a custom mountain bike frame, “It is basically a BMX with 26” wheels.”

His style is tig-welding in steel and occasionally some titanium if it is called upon. Instead of using a standard tube-set bought from one supplier, Seth had used his keen eye for detail and selected tubes from various suppliers each chosen for its individual properties. In addition, he specifically machines them – external butting to reduce weight, internal butting to add strength in the right places – and uses an oversized press-fit BB shell. As he explained his process, geometry and testing system, the tubing clamped in the welding jig changed from being raw cylinders of steel, I realised I was looking at a very special bicycle frame. Seth is the opposite to Johnny, loving the challenge of building different styles of frames. Hanging on the wall are BMXs, mountain bikes and a tough looking fixie. The overarching theme is that they are aimed at aggressive riding styles – be it street messengers, cyclocross racers, mountain bikers or dirt jumpers. Softly spoken, yet sharply determined, the scars of piercings gone-bye and an occasional tattoo, Seth has clearly been mixing with the right crowd and is an old-dog in the ways of breaking bikes and building better frames.
On the other side of town Marty Odlin is just about to hop on a bus to join his team who have hit the road in a touring van running bike building workshops all around the country. We chat on the side-walk while the bus driver gets more and more anxious. Marty started Bamboo Bikes five years ago, “It came about through a collaborative process, we experimented at making bamboo bikes with our friends, and came up with this process. Therefore I don’t consider it to be mine to own or belong to anybody”.
In an industry that sometimes shrouds its knowledge in secrecy and mystique, Marty has gone in completely the opposite direction. Bamboo Bikes aim is to educate and spread the knowledge about how to build simple bicycles using sustainable materials available to us all. The workshops will soon be accompanied by on-line do-it-yourself kits and free to download instructions. It was refreshing talking to him and understanding that by being completely open much in the same way as some ‘open-source’ computer programs, they are in-fact benefiting themselves. “I would love to teach pods of Bamboo-bike builders to be able to pass on the skills and knowledge around the country” and that is exactly what he is setting about doing with his touring van, if he can catch-up with it in time!
Walking down what may as well have been Sesame Street somewhere in Harlem, I counted the barred gates leading into basements and bowed my head into what turned out to be a subterranean Tardis. Ezra Caldwell has been running Fastboy Cycles for four years. With a background in carpentry, he started making wooden fenders and racks for people customising their own bikes. His basement is divided between a dusty woodwork shop, and a sparkly clean machine shop. Each tool and machine has its place and every modicum of space is utilised to allow smooth workflow and efficiency. Ezra’s deep desire to provide the whole product and not just components to adorn existing bicycles, saw the move across into building frames as a natural progression. Having been a professional dancer he had oodles of creativity but always struggled with unnecessary extravagance. This has been expressed through his functional mountain bike and road frames that balance form and function succinctly.
Most New Yorkers struggle for space living in cramped apartments but for Ezra, their dependence on cars bothered him, particularly the short journeys they made around the city in them. A bike capable of running everyday errands would be ideal but most cargo bikes are too big to fit in an apartment, would be stolen if locked up outside an apartment, and are too heavy to carry up stairs into an apartment. Ezra solved the problem by designing a unique load carrying bike styled on a mountain bike for easy handling, low weight, and keeping a short compact frame. The same length as a mountain bike but with 20” front wheel gives room for a cargo box to sit above capable of holding 40lbs or the equivalent of an apartment full of groceries. His bicycle provides the New Yorker with a real alternative to the car. “It’s designed by a New Yorker, built by a New Yorker, intended for a New Yorker.”
Joe Avendisian opened the non-descript blue door to Brooklyn Machine Works, a large grin and outstretched hand welcome me into his machine shop. I notice his wrist is sporting recent scars which he later tells me are from snapping his wrist when he over jumped a ramp at a mountain bike park – at 44 he is still living his dream. Starting in 1984 selling BMX frames to friends, BMW followed a natural progression coming up with innovative solutions for bicycles. Joe made a name for himself building some of the first long travel Down Hill specific mountain bikes. His original design from the mid-nineties is still in production and are renowned for being ultra-resilient. “Yeah, I see frames come in for their third or fourth coat of paint. They are really tough to smash-up.” Employing a couple of skilled welders, BMW make a range of 20” BMX, 24” dirt jump, 26” Mountain bikes, All Mountain, and DH bikes. Not afraid to try new things, the walls are lined with prototypes of years gone by. He shows me brakes, tyres, pedals and all manner of frames that he has given a go and was quick to send me out on his most recent frames for a quick test ride.
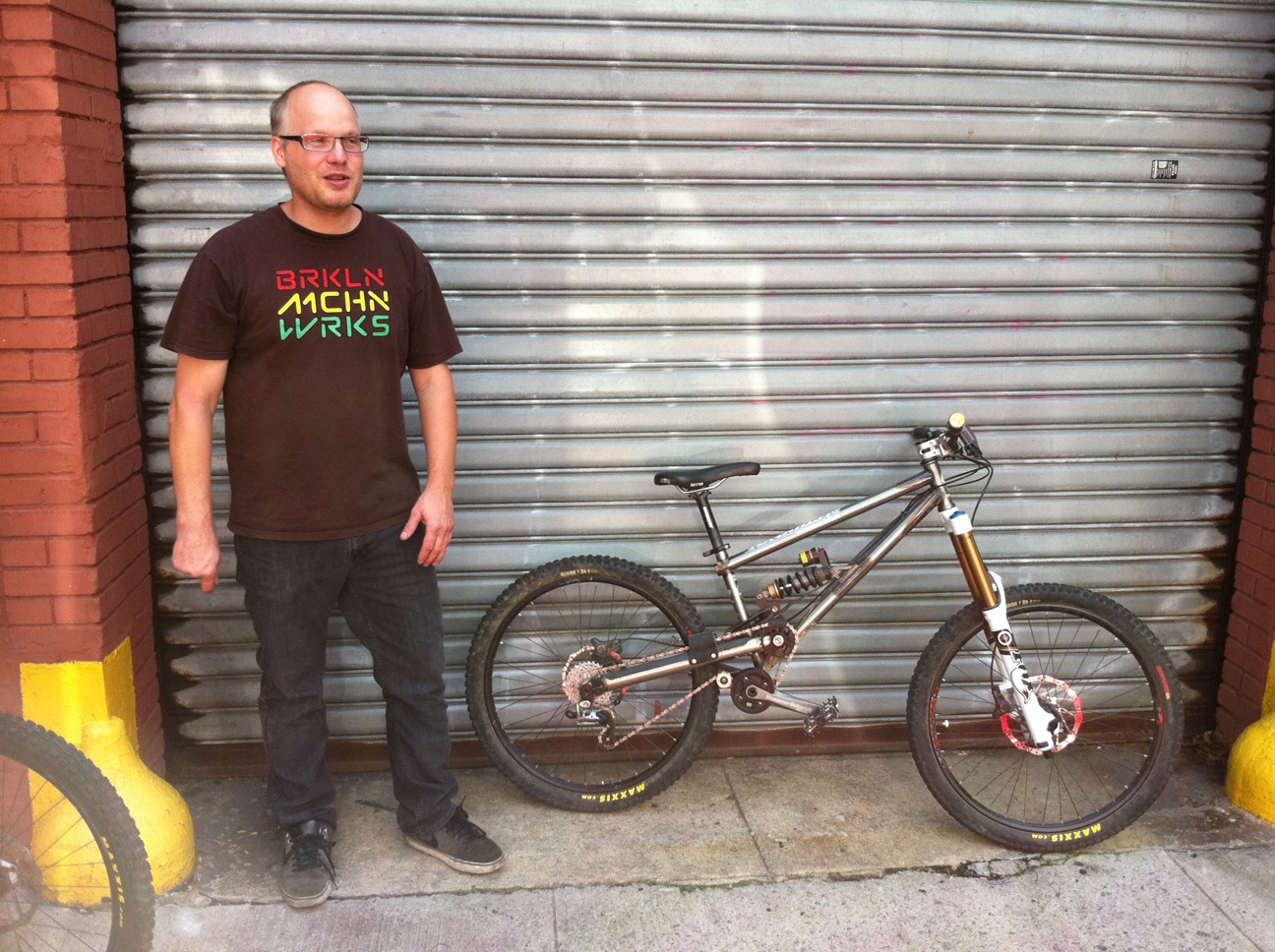
Recently Joe had a revelation. “I’d been building our tough fixie frames aimed at street riders and trick jumpers, they were not particularly well accepted, with most opting for traditional track style frames, but we persevered. All of a sudden, as we had predicted they went crazy, everyone wanted one.” Joe had connections into Taiwan and realised that the limitations he had been pushing against with his workshop facilities were suddenly gone and his creativity could expand with the manufacturing techniques available to him in Taiwan. “Laser-cut tubing was the first thing I was able to take advantage of,” showing me an internally butted head tube cut by laser that would be massively time consuming and difficult to machine in house. Still using the best quality steel tubes but sourced at a lower cost he is able to include new innovations in the frame design resulting in better quality, stronger frames at a lower cost. “I can provide an even better product at a cost which more people to be able to afford and my bikes can be ridden even longer!” Excited about the new opportunities Joe’s business is changing. “I will still make custom frames for individual riders, our mountain bikes will still be made here in Brooklyn, we will still innovate new frames and products, but BMW will have its own retail outlet for its own parts, apparel and our awesome new bikes designed by me and the feedback I get from my riders.”
I see frames come in for their third or fourth coat of paint. They are really tough to smash-up.
I decide to walk the couple of miles through Brooklyn past the project commission buildings and through streets once ruled by the gangs and drug dealers. No longer the case; people walk past going about their business and to my surprise lots are happily cruising around on bicycles. The car might be king of Manhattan but it’s no longer quite the king of Brooklyn.
My last meeting is with SquareBuilt. As I walk down the steps into another basement workshop I sense an air of tomfoolery, it’s Friday afternoon and the replacement order of Argon Gas used in their welding equipment hadn’t arrived, beer o’clock struck its hour early and a plastic cup full of whiskey is thrust into my hand. Lance had gone through the UBI frame building course and had sold his super tough frames to local friends, before he knew it he had a frame building business. Alex, his assistant welder explained that they could do just about anything, showing me examples of touring frames, repair jobs and special one-offs but where SquareBuilt’s passion lies is in making tough durable bikes for messengers, polo players, and street riders.
Their rough and tough attitude was crystalised when ‘Tone’ dropped in, a professional messenger Tone rode his SB through everything. Everyday he would slam it against poles, drop his lock onto the frame, bounce off the occasional taxi and generally abuse his hand-built custom bike. “What’s the point of using an exotic piece of lightweight ultra-thin tubing when our bikes are given that sort of treatment? We like our bikes to be ridden hard and not put in a glass case to be admired. The best compliment is seeing people like Tone come in with beat-up bikes knowing that my frame is doing its job and is out there being ridden hard.” With a can-do attitude Lance powder coats his frames in his home made powder booth and pulls a set of very trick looking BMX style handle bars off the powder rack. These are for the messenger and polo riders whose bikes are always getting hit and dropped. Standard bars are not up to the rigours without folding or getting dinged. With straight-gauge thick walled steel and a slight rise, these bars are as tough as nails. “We saw what was happening out there with bars all smashed up and thought we could do something better.” Tone finishes up and gives Lance and Alex a crazy-assed hand shake which has us all in stitches the evening degenerates into bike talk, stories of riding daring-do and of course more whiskey.
I went to New York to find out about the types of frames the local frame builders were making and how they made a living in a culture that was so dependent on motorised transport. What immediately struck me about all of them was their warmth and openness. They love what they do and are happy to talk about how they do it. They’re also passionate about advocating for more people to get out and enjoy riding. They are entrepreneurs who have sought niches in a hard market that they are softening by providing value and service with their own individual styles. They have low cost set-ups and all of them are in the process of growing, each with their own ideas and direction but more importantly, they have taken the courage of their convictions and are actually doing it. New York is always changing and there is a growing culture of frame designers identifying bicycle riders’ needs, solving problems and coming up with smart solutions. The frame designers I met are there making it happen.
Ride On content is editorially independent, but is supported financially by members of Bicycle Network. If you enjoy our articles and want to support the future publication of high-quality content, please consider helping out by becoming a member.
Great article, kept my interest from beginning to end, spare with words but not overly so – like a well built frame. Enjoyed the insight into New York life that it gave me. – Dad.
Need to know if u can weld on track drop out on a mountain bike